Firstly, there is the heritage of the Stratos to consider – now entering its third generation. But not many people know that the first Schmidt salt spreader was actually designed and built in Holten in the Netherlands way back in 1949. So we have a heritage with the machine going back almost 70 years.
Each generation has been built based on continuous customer feedback so that in theory, and we hope, in practice, every version is better than its predecessor. Each year the Aebi Schmidt Group spends millions on research and development, while Aebi Schmidt engineers carry out numerous CAD simulations to model how the machine will perform over its expected life.
We also benefit from what we describe as ‘resilience through experience.’ That means that we benefit from the experiences and feedback from different regions and markets around the world, often in areas where conditions are extremely inhospitable. That gives us the confidence that if the machine operates well in Norway, it is just as likely to do so in London, Munich or Paris!
At the same time, we are very proud of the build quality of the Stratos. Not only is it a very impressive-looking machine, but it oozes quality from every angle. Because of the highly corrosive nature of salt, it is made from the highest quality materials, including powder coated or stainless steel and high quality polymers, for a really first class build quality.
This quality is continued by the use of robot welding in the factory, with all seams being double welded, inside and out, to ensure there are no areas where a build up of salt can occur and start the corrosion process.
This keeps the machine looking good for its expected life span of at least 10 years and we usually expect the chassis it is mounted on to perish before the actual spreader itself.
Another plus is the commonality of parts across the Stratos range, from the smallest demountable spreader to the largest permanently mounted pre-wet spreader. This gives the benefit of ease of parts replacement, straightforward maintenance and low costs.
The Stratos has been deliberately designed with ease of maintenance and low costs in mind. It is easy to wash down and maintenance points are very accessible for greasing, while our Evolution Smart (ES) control panel, the nerve centre of the machine, also operates as a diagnostic tool, readily identifying and warning of any faults as they occur.
Another of its key plus points is the accuracy of spreading, and the machine uses a closed loop hydraulic system to operate the conveyor belt and the spinner independently of each other. The ES control panel monitors the machine at a rate of 2,000 times per belt revolution and makes continual adjustments at 100 times per second to ensure accuracy is maintained. All of the time, these adjustments are fully road speed-related.
Having the right dosage levels of salt is paramount in ensuring the safety of road users at all times, and especially in extreme conditions, while reducing salt levels is important from a cost efficiency basis. At the same time, there are sound environmental benefits from only spreading the exact amount of salt required because of its highly corrosive nature. So accuracy of spreading quantities is of vital importance and this is a key aspect of the Stratos’ operational efficiency. Another key benefit of the Stratos, as we have already mentioned, is its state-of-the-art ES control panel, which really controls everything the machine does. The advanced nature of the system means that not only can the Stratos be controlled in a precise and safe manner, but that the control panel also acts as a diagnostic, calibration and remote access service tool.
The ES control panel integrates seamlessly with the optional Schmidt AutoLogic system – an easy to use, automatic spreading system with GPS-guided routing. The GPS navigation guides the spreader driver along the correct route and the spreading settings occur automatically, enabling the driver to fully concentrate on the traffic without being distracted by the spreading process, thus increasing road safety.
Another option is the Schmidt Winter Report, a web-based telematics system which shows the user where the spreader has been and where it is currently spreading in real time. It is fully integrated with the ES control panel, requiring no other hardware or software, and giving just one point of contact.

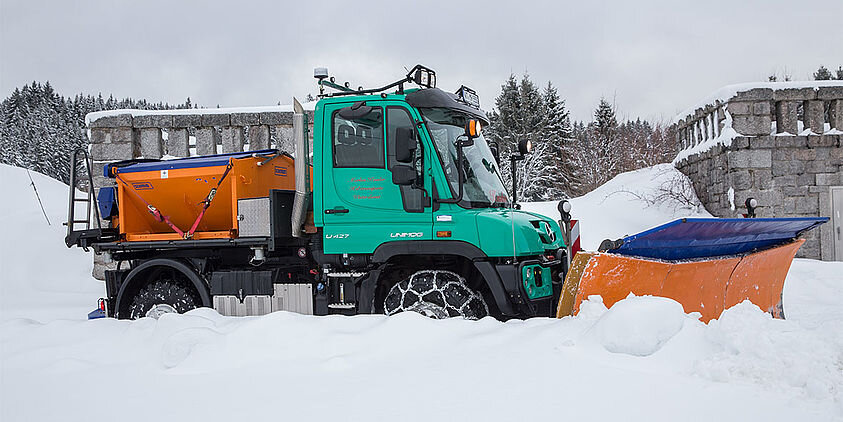
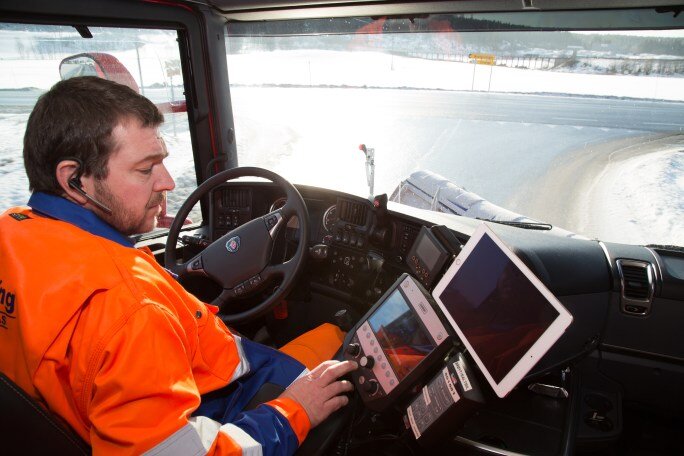

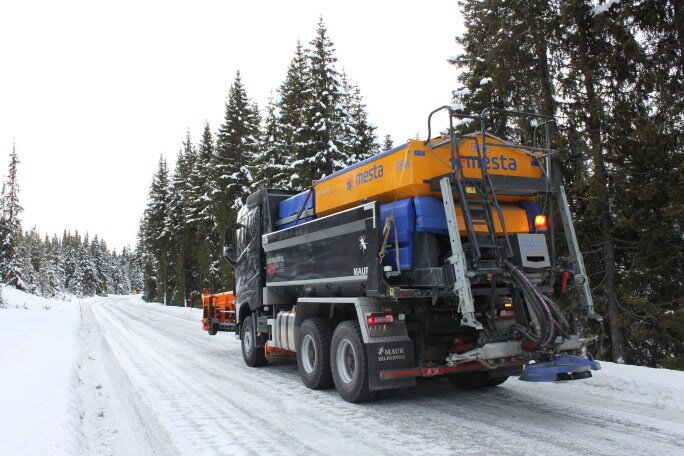